Automotive wiring harness industry situation
Automotive wiring harness enterprise layout
Overseas wiring harness giant layout of the whole industry chain, domestic enterprises are based on assembly.
Overseas giants have the ability of the whole industry chain, and domestic cables, connectors and wiring harnesses have enterprise layout, but no enterprise has the whole industry chain layout.
Automotive wire harness industry high barriers
The automotive wiring harness industry has four major barriers of suppliers, technology, capital and management. Among them, the management barrier is particularly important, the auto wiring harness production process is complex, the process before and after a total of 17 steps, so production management and cost control is very important.
Aichie: Custom Automotive Wiring Harness
Automotive wiring harness industry chain
The upstream and downstream industry chain of the automotive wiring harness industry covers many links such as raw material supply, wiring harness manufacturing, and vehicle supporting. Next, the industry chain of the automotive wiring harness industry will be analyzed from three aspects: upstream raw materials, midstream manufacturing and downstream applications.
1. Upstream raw materials - stable supply
The main raw materials of automotive wiring harness include copper, aluminum, plastic, rubber and so on. At present, the supply of these raw materials is relatively stable with little price volatility. Labor costs account for about 12%-17% of total production costs, and raw materials account for 70-80%. With the gradual recovery of the global economy and the continued prosperity of the automotive market, upstream raw material suppliers are also expanding their capacity to meet the needs of the market. At the same time, some raw material suppliers are also actively developing new materials to improve the performance of automotive wiring harnesses and reduce costs.
2, midstream manufacturing - fierce competition
The manufacturing link of automobile wire harness is the core part of the whole industry chain. At present, the number of domestic automotive wiring harness manufacturing enterprises is large, but most of the enterprises are small and the technical level is uneven. In order to gain a foothold in the market, some enterprises have begun to increase investment in research and development to improve product quality and performance. At the same time, some powerful enterprises also expand production scale and increase market share through mergers and acquisitions and other ways. However, with the intensification of market competition, the cost pressure of manufacturing links is also increasing.
3, downstream applications - demand diversification
The downstream applications of automotive wiring harnesses mainly include traditional fuel vehicles, new energy vehicles and various commercial vehicles. With the continuous development of the automotive market, the demand for automotive wiring harnesses in downstream applications has also shown diversified characteristics. The demand of traditional fuel vehicles for automotive wiring harness mainly focuses on the basic electrical connection and signal transmission; New energy vehicles put forward higher requirements for high-voltage wiring harnesses and battery management system wiring harnesses. Commercial vehicles pay more attention to the reliability and durability of the harness. These diverse needs provide a broad development space for the automotive wiring harness industry.
Automotive wire harness industry chain investment core logic
1. Electrification
New energy vehicles have spawned the use of high-voltage wiring harnesses. Compared with traditional fuel vehicles, the drive voltage of new energy vehicles is higher, and high voltage wiring harnesses are required to connect each circuit unit.
In new energy vehicles, The high voltage harness is mainly used for the high voltage harness of the power battery (connecting the power battery to the high voltage distribution box), the motor controller harness (connecting the high voltage distribution box to the motor controller), the fast charging harness (connecting the fast charging port to the high voltage distribution box), the slow charging harness (connecting the slow charging port to the car charger), the high voltage accessory harness (connecting the high voltage distribution box to the DCDC, the car charger, and the air conditioning compression Machine, PTC) 5 parts.
High Voltage Cable Harness
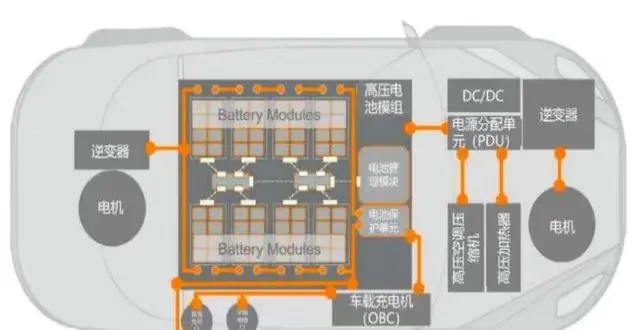
EV high voltage wiring harness use parts
High voltage wiring harness puts new requirements on the wiring harness industry. New energy vehicles have higher requirements for wiring harness conveying capacity, mechanical strength, insulation protection and electromagnetic compatibility.
(1) The rated power of the motor used in new energy vehicles can generally reach 150Kw, and in order to minimize the energy loss of the current in the transmission process, it is necessary to improve the working voltage of the high-voltage electrical system, the driving voltage can generally reach about 550V-750V, and the fast charging voltage can even reach 800-1000V. It is much higher than the 12V voltage of fuel vehicles, so the wiring harness is required to have stronger pressure resistance and tightness to avoid the high-voltage cable short circuit after the collision of the car and cause combustion accidents.
(2) The application of new energy vehicles is AC motor, electromagnetic interference is relatively strong, and the design of new energy vehicles must consider electromagnetic interference to ensure the reliability of wire harness application.
(3) The transmission of large current will inevitably lead to high power consumption and heat, and the design of high-voltage wiring harness must choose materials that can withstand higher temperatures.
The value of new energy vehicle wiring harness bicycles has increased significantly. The high-voltage wiring harness system is a new system under the electrification, replacing the engine wiring harness of the traditional car, and the value of the bicycle can reach 2000 yuan, thus driving the total average bicycle value of the new energy vehicle wiring harness to reach more than 5000 yuan, and the maximum can reach more than 10,000 yuan, which is significantly higher than the average level of 3,500 yuan for fuel vehicles.
2. Intelligence
Smart cars are constantly being upgraded. The state actively encourages the development of intelligent driving industry, the Ministry of Industry and Information Technology "intelligent connected vehicle technology roadmap 2.0" proposed that by 2025, PA(partial autonomous driving), CA(conditional autonomous driving) intelligent connected vehicles market share of more than 50%, HA(highly autonomous driving) intelligent connected vehicles to achieve limited areas and specific scenarios of commercial application; By 2030, the market share of PA and CA intelligent connected vehicles will exceed 70%, and the market share of HA intelligent connected vehicles will reach 20%, and it will be widely used in highways and large-scale application in some urban roads. In terms of driving comfort, the penetration rate of intelligent cabin functions such as intelligent large screen, HUD, voice and gesture recognition, seat and steering wheel heating is also increasing, and these functions all rely on wire harnesses to ensure signal transmission.
Intelligent upgrading promotes the use of wiring harnesses. As automotive intelligence increases, sensors and computing become more sophisticated and complex, and software-defined vehicles become more prevalent, the bandwidth requirements for data connectivity are growing rapidly and beyond the reach of traditional in-vehicle network performance. According to the forward-looking Economist data, the current average number of automotive sensor equipment more than 90, the number of high-end models of equipment up to 200, safety and intelligent driving demand will promote the number of automotive sensors continue to grow, thereby promoting the growth of wire harness usage. In addition, the improvement of automatic driving function puts forward new requirements for high-speed data transmission, which drives the demand for high-speed transmission data cables, and high-frequency high-speed wiring harnesses for vehicles are mainly used for cameras, sensors, antennas, GPS, Bluetooth, WiFi, navigation and auxiliary driving systems.
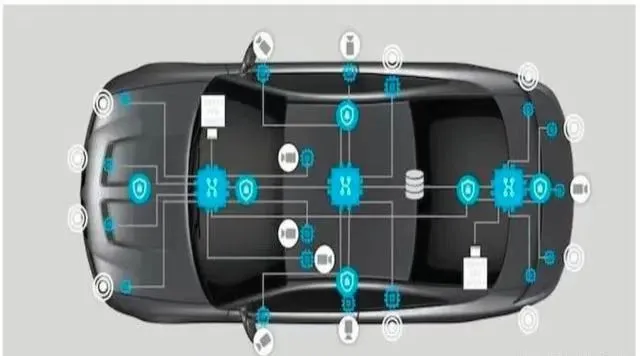
high-frequency high-speed wiring harnesses uses parts
3. Localization
The localization of automobiles will drive the localization rate of automobile wiring harnesses. Since 2020, the market share of Chinese self-owned brands in passenger cars has increased year by year, reaching 56% by 2023. The local parts procurement rate of independent automobile brands is high, and the steady improvement of its market share will certainly bring opportunities for the development of local automobile wiring harness enterprises.
Lightweight has become the development direction
Lightweight has become a development trend, but whether aluminum will gradually replace copper, this also needs to improve technology and the market to verify. In the context of global environmental standards continue to strengthen, in order to improve the fuel efficiency of vehicles, car manufacturers are vigorously promoting the production of lightweight vehicles.
Body weight reduction will optimize the fuel economy, handling stability and crash safety of the vehicle, and effectively improve the quality of the vehicle. According to statistics, for every 10kg reduction in the weight of pure electric vehicles, the driving range can be increased by 2.5km. In 2020, the "Energy Saving and new energy Vehicle Technology Roadmap 2.0" issued by the Ministry of Industry and Information Technology pointed out that by 2030, the weight of vehicles should be reduced by 35% compared with 2015. As an important part of the car, the mass of the car wiring harness accounts for 2%-3% of the total mass of the vehicle, while the car cable accounts for 75%-80% of the weight of the car wiring harness, to estimate the weight of a B-class car, the weight of the wire is about 25-30kg. Affected by this, the lightweight development of automotive wiring harnesses has also become a key breakthrough area.
At present, with the rapid development of automobile electronization and information technology, the large number of electronic equipment in the car makes the electric wiring in the car longer and more complex, the increase in the weight of the car wire harness also leads to the increase in the cost and energy consumption of the vehicle, and the lightweight development goal of the wire harness becomes more and more important.
The development of automotive wire harness lightweight is mainly reflected in the three sub-components of wire, connector, and wire harness protection, and the specific optimization methods include power cord and signal wire material optimization, structural optimization such as connector, and plastic replacement of metal and other materials and design optimization. The main raw material of the current cable is copper, which is the key weight reduction direction. In terms of weight reduction of automotive wire harness products, in addition to the extensive use of thin-wall wires to reduce the cross-sectional area of wires, the use of aluminum, which is lower in cost and lighter in weight than copper, has become a hot research and development direction of wire harness lightweight, and the density of aluminum is only 30% of copper. In the future, once there is a mature solution to the problems of easy oxidation of aluminum wires and unstable electrical and mechanical properties, lightweight aluminum wiring harnesses are expected to become the main technical route for automotive wiring harnesses.
At present, it is understood that Tesla and Millet SU7 use aluminum wiring harnesses, and the high-voltage wiring harnesses used by domestic mainstream new power manufacturers are copper. Only Tesla publicly advertises its use of all-aluminum high-voltage wiring harnesses. The industry generally believes that on high-voltage wires, Tesla uses high-voltage aluminum wires, which are 21% lighter and cheaper than copper wires with the same flow capacity. Musk has publicly advertised that Tesla uses aluminum wire harness so that the cost is lower, and Tesla's wire harness length is only about one-tenth of the traditional, so cost savings while reducing weight.
The two wires have the same carrying capacity, the quality of the copper wire is about twice that of the aluminum wire, coupled with the difference in the price of copper and aluminum, the final equivalent copper wire cost is about 7 times that of the aluminum wire. It is worth noting that due to the relatively large cross-sectional area of aluminum wires under the same conditions, the demand for materials such as insulation and protection of aluminum core cables increases, which correspondingly reduces the price advantage of aluminum wires. At present, the price of aluminum alloy cables commonly used in the market is only about 75% of copper core cables. If the continuous current of the same size is required, 50 square copper wire can be replaced with 70 square aluminum wire, even so, the weight can still be reduced by about 45%, and the cost can be saved by more than half.
The competitive situation of the automotive wiring harness industry
Global market pattern
At present, the global automotive wiring harness industry is dominated by foreign investment. The contribution of high-voltage wiring harnesses, the Chinese wiring harnesses market is the main increase, the top three in the global automotive wiring harnesses market can reach 71%, Yazaki, Sumitomo, Ambofu accounted for 30%, 24%, 17% respectively. China's automotive wiring harness market in 2022 market size of 81.46 billion yuan, an increase of 5.5%. According to the statistics of Huajing Industrial Research Institute, the top seven enterprises in the global wiring harness industry in 2021 are foreign capital. At present, the global competition pattern is mainly dominated by German, Japanese and American giants.
Domestic market
The domestic market is more dispersed, the customer localization trend is obvious, overseas brands account for a relatively high proportion, such as Honda, Toyota, Nissan and other Japanese car companies the main suppliers are Japanese manufacturers, such as Sumitomo Electric, Yamazaki and so on. Lenny, Amboffo, Decosmeer are mainly connected with most German and American brands. Joint venture wire Harding enterprises mainly support SAIC Volkswagen, FAW-Volkswagen and other joint ventures, such as Keserun (derun Electronics & Koberschutt joint venture), Keserke (Coboda & Koberschutt joint venture), Suzhou Potney (Shanghai Jinting (Yongding subsidiary) & Sumitomo joint venture).
The number of independent brand car wiring harness manufacturers is large, most of them are small, the research and development capacity is weak, the production equipment is backward, the quality grade is not high, the supporting model is single, mainly for the supporting processing of independent car enterprises, and the market share is high in Tianhai, Huguang and so on.
The advantage of foreign/joint venture brand is that the product quality is high, the production is stable, but the price is higher. With the gradual development of domestic car companies and the increasing attention of international car companies to cost control, the localized procurement of auto parts is increasingly strengthened, local brands have advantages in price and gross profit, and are closely linked with domestic Oems, relying on the rapid development of domestic new energy vehicles and seize the market. Some leading wiring harness enterprises that have established brand influence in the high-end and high-quality wiring harness market have begun to accelerate the layout of industrial capital, integrate industrial resources, give full play to the synergistic effect with partners in technology, customer resources and supporting services, and the domestic substitution space is large.
Supplier qualification requirements are strict, and the industry faces the survival of the fittest. Oems often establish strict certification evaluation standards for automotive wiring harness suppliers, in general, automotive wiring harness enterprises want to enter the parts supporting system of Oems, not only must first pass the IATF16949 quality management system standard certification developed by the International Automotive Working group, It is also necessary to meet the special standards and requirements of vehicle manufacturers in product quality, synchronous development, logistics and transportation, management level, cost control, financial status and other aspects.
In the future, with the development of the automotive industry, automobile manufacturers have more stringent and complex requirements for automotive wiring harness products, smaller and weaker wiring harness enterprises will face a more severe market environment, and China's high-quality wiring harness enterprises will rely on outstanding product quality and stable customer resources to further expand market share. In the future, China's wire harness industry will face the survival of the fittest and accelerate the realization of resource integration of the industrial environment.
The rise of domestic cars will drive the localization rate of automotive wiring harnesses. Since 2020, the market share of Chinese self-owned brands in passenger cars has increased year by year, reaching 56% by 2023. The local parts procurement rate of independent automobile brands is high, and the steady improvement of its market share will certainly bring opportunities for the development of local automobile wiring harness enterprises.
Aichie Tech provides auto wiring harness , high voltage ev cable assembly and low -voltage auto wiring harness around the world. It has introduced new production equipment, which greatly improves the quality and efficiency of production. Customers are widely distributed in Europe and North America. Production employees and experienced engineering teams and sales teams serve our customers; please contact us now! We will provide you with competitive prices!
E: sales03@aichie.com
WeChat: 180 2750 2150
Tel: +86 180 2750 2150