The Weather Radar Lattice Tower Introduction
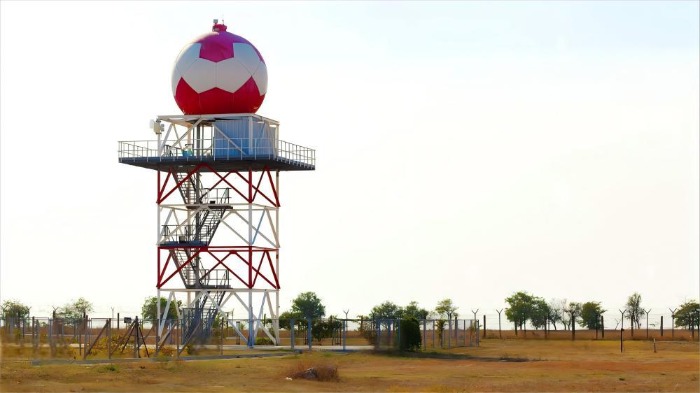
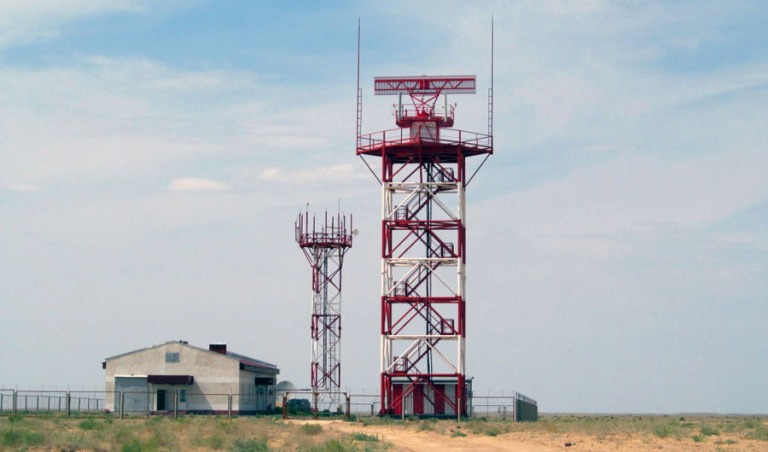
Choosing the right circular saw blade for your cutting needs involves considering various factors, including the number of teeth on the blade. The decision between more or fewer teeth on a circular saw blade, such as the Metal Saw Cutter or Toothed Round Cutter, depends largely on the material you're cutting and the desired cut quality.
Understanding Tooth Count:
Circular saw blades come with different tooth configurations, typically ranging from fewer teeth (for faster, rough cuts) to more teeth (for smoother, precise cuts). HSS Slitting Blade are commonly used in metalworking applications, each designed to optimize cutting performance based on the material's hardness and thickness.
When to Use More Teeth:
1. Precision Cutting: Blades with more teeth are ideal for materials like metals, where a clean, precise cut is crucial. HSS Slitting Blade with higher tooth counts produce smoother edges, minimizing the need for secondary finishing.
2. Thin Materials:When cutting thin materials, more teeth help distribute cutting force evenly, reducing the risk of material distortion or burrs. This is particularly useful in applications requiring high accuracy.
When to Use Fewer Teeth:
1. Faster Cutting:Blades with fewer teeth are suitable for rough cuts or thick materials, where speed is prioritized over finish quality. These blades remove material quickly but may leave rougher edges.
2. Less Heat Buildup:In some applications, fewer teeth can reduce heat buildup during cutting, prolonging blade life and improving overall efficiency, especially in high-volume operations.
Choosing the Right Blade:
Consider the following factors when selecting a circular saw blade:
Material Type:Different materials require specific tooth configurations for optimal performance.
Cutting Speed:Balance between speed and finish quality based on project requirements.
Blade Maintenance:Regular maintenance and blade sharpening ensure consistent performance and longevity.
By carefully selecting between more or fewer teeth on your circular saw blade, you can enhance cutting precision, improve efficiency, and achieve superior results in your metalworking projects.
There are various types of sliding door hardware kits available in the market to suit different requirements and design preferences.
Top-mount sliding door hardware kit
This type of kit features a track mounted on the top of the door frame, allowing the door to slide smoothly along the track. It is commonly for heavier doors and offers excellent stability and weight-bearing capacity.
Bottom-mount sliding door hardware kit
Bottom-mount sliding door hardware kit is designed with a track that is installed on the floor, providing support for the door to glide smoothly. It is often used for lighter doors or applications where a sleek and minimalist appearance is desired.
Wall-mount sliding door hardware kit
Wall-mount sliding door hardware kit is fixed to the wall adjacent to the door opening, allowing the door to slide horizontally along the wall. It is ideal for spaces with limited ceiling or floor space and provides a modern and space-saving solution.
Bypass sliding door hardware kit
Bypass sliding door hardware kit is specifically designed for sliding doors that overlap each other when opened or closed. It allows multiple doors to slide past one another, making it suitable for closets, wardrobes, or rooms where space efficiency is crucial.
Barn door sliding hardware kit
Inspired by traditional barn doors, Barn door sliding hardware kit features a rustic and stylish design. It typically includes a track, hangers, and other necessary components for hanging the door. It adds a unique and aesthetic appeal to any space.
These different types of sliding door hardware kits provide flexibility in terms of installation, functionality, and design options. They facilitate smooth and effortless sliding motion, enhancing the overall convenience and visual appeal of sliding doors in various residential and commercial applications. We are professional sliding door hardware manufacturer, get more details from https://www.shrjrov.com.
Water infiltration poses a significant threat to the structural integrity of construction projects, especially in environments exposed to rain, humidity, or other water-related challenges. Closed end blind rivets, renowned for their secure and efficient fastening capabilities, also offer impressive waterproof properties that make them a preferred choice in diverse construction applications. This article delves into the unique features of closed end blind rivets that contribute to their effectiveness in creating a watertight seal.
Sealed Construction:
Closed end blind rivets, also referred to sealed blind rivets, are specifically engineered to have a sealed end, distinguishing them from open-end rivets. This sealed construction prevents the ingress of water through the rivet, making them an excellent choice for applications where maintaining a waterproof barrier is crucial. The closed-end design ensures that the fastener itself becomes a reliable defense against moisture penetration.
Protection Against Corrosion:
The sealed nature of closed end blind rivets not only safeguards against water but also provides an added layer of protection against corrosion. Moisture is a common catalyst for corrosion, and by preventing water from reaching the internal components of the joint, closed end blind rivets help extend the lifespan of the fastening connection. This corrosion resistance is particularly valuable in outdoor or marine environments.
Ideal for Exterior Applications:
Construction projects often involve elements exposed to the external environment, such as metal roofs, siding, or outdoor structures. Closed end blind rivets, as a watertight blind rivets, shine in such applications, offering a watertight seal that enhances the weather-resistance of the joint. Their ability to withstand exposure to rain, snow, and other external elements makes them a reliable choice for projects where maintaining a waterproof seal is paramount.
Reliable in High-Moisture Environments:
Closed end blind rivets excel in environments characterized by high humidity or frequent exposure to moisture. Whether used in boat construction, outdoor signage, or HVAC systems, these rivets provide an effective barrier against water intrusion, preventing issues such as mold growth, rust, and degradation of materials.
Ease of Installation and Inspection:
The installation process of closed end blind rivets is straightforward, and the sealed design contributes to the ease of inspection. Visual checks can be conducted to ensure the integrity of the riveted joint, providing reassurance that the watertight seal remains intact. This ease of inspection is particularly valuable in applications where regular maintenance and monitoring are essential.
Closed end blind rivets stand as a formidable solution for construction projects seeking effective waterproofing properties. Their sealed construction, protection against corrosion, suitability for exterior applications, reliability in high-moisture environments, and ease of installation make them a preferred choice for professionals aiming to fortify their structures against water-related challenges. As construction standards continue to emphasize durability and resilience, closed end blind rivets emerge as a crucial component in the arsenal of waterproofing solutions, ensuring the longevity and reliability of diverse construction projects.
The metal casting process can create anything from tiny fasteners to large industrial components, all through a five-step procedure. It happens by creating a pattern and making a mold, melting and transferring the metal and finishing, cleaning, polish and inspecting the casting. While metal casting is a straightforward practice, it requires specialized skills and techniques to perfect.
At Hengchang Foundry, we have the mastery and technology to form objects of various sizes for different industries like heavy equipment and transportation. No matter the complexity of the parts you require, our professional team can produce tailored castings to deliver unique parts for your application.
What is the metal casting process? Continue reading to learn what to know about metal casting and how our metal casting services work.
When talking about a pattern, we aren’t referencing one you trace on a piece of paper. Instead, metal casting foundries refer to patterns as a replica of the object they’re casting. This pattern helps form the mold cavity, which can be made of wood, plastic, aluminum and many other suitable materials. Making a pattern is a crucial first step because the accuracy of the mold determines the accuracy of the final product.
The four steps in producing a precise pattern include:
Depending on the type of material being poured into each mold, the final, solid product will distort to a certain degree. For example, it may shrink compared to the original size of the mold. This is why each pattern has allowances for slight alterations. Additionally, patterns require a draft, or a vertical tapered wall, where professionals can extract the pattern without tampering with the molded product.
It’s now time to create the mold, which is a hollow shape that will form the metal later on in the process. While some molds are expendable, others are nonexpendable.
An expendable mold means you can’t use it again. In that case, materials like sand, plaster foam or plastic make up the mold, and they’re destroyed during the casting process. Alternatively, you can use nonexpendable molds indefinitely, as they’re often made of aluminium.
Both expendable and nonexpendable molds can support different pattern complexities and materials.
While we use a multitude of materials for metal casting, they all fall under one of two categories — ferrous and non-ferrous metals. The metals used in metal casting can include iron, zinc, aluminum, tin, copper, lead alloys and others. While a ferrous metal contains malleable iron or steel, a non-ferrous metal contains nonmalleable metal, such as copper, nickel or aluminum.
After selecting the appropriate metal type, we load it into the furnace where temperatures rise until it reaches the material’s melting point. At Warner Brothers Foundry Company, we use gas furnaces during the metal casting process, though there are two other common types of furnaces for metal casting — electric arc and induction.
Using electric furnaces is our preferred method for metal casting because it burns cleanly and efficiently. Electric furnaces also allow us to heat the metal to the necessary temperatures without using high amounts of electricity. Electric furnaces are more efficient for our process, which keeps costs lower on our end and allows us to offer lower prices on your end.
Once the material melts down, it’s transferred to a large ladle before it reaches the mold. Through gates and risers, or openings in the mold, workers or machines pour the liquid material into the mold. Once it takes shape, solidifies and cools, we eject the casting from the mold, removing excess metal from the gate and rider system before moving to the next step in the process.
Understanding how long metal casting takes depends on the material — some may cool within minutes, and others take several days.
This stage involves making the final touches and cleaning each individual part. At Hengchang Foundry Company, we go in and remove excess metal parts and begin the cleaning process, using different tools to clear away particles and dirt. The final product is the same proportion and shape as the original pattern used during step one.
Additionally, some products may require a heat treatment, such as rail clamp, hydraulic cylinder, buffer. This process alters the properties of the material through a heating and cooling technique where the metal becomes more resilient. These treatments are ideal for applications that may endure extreme weight, wet environments or freezing temperatures.
The metal casting process ends with an inspection to ensure everything is complete and up to our standards. During the final stage, we check the part’s physical structure and integrity to ensure it’ll hold up and perform the expected job.
There are destructive and nondestructive testing methods, which are put in place depending on the casting’s specifications. In particular, visual inspections include looking for cracks, accuracy and surface finishes, and more in-depth testing checks tensile strength, hardness and ductility, among other components.
No matter the industry, we inspect everything from trailer hitches and industrial equipment to small automotive parts. In the end, you’ll have a durable component that’s suited to your unique needs and operations.
Welcome to KYNKO, your go-to destination for high-quality angle grinders! As a leading Chin manufacturer specializing in power tools, we understand the importance of selecting the right equipment for your projects. In this guide, we will provide you with valuable tips on choosing the perfect angle grinder to meet your needs.
An angle grinder is a handheld power tool mainly used for grinding, cutting, polishing and sanding various materials.
1. Power Requirements: Consider the power of your angle grinder based on the tasks you want to perform. For lighter tasks such as polishing or sanding, a low-powered grinder will suffice. However, for heavy-duty cutting or grinding, choose a higher wattage to ensure optimal performance.
2. Wheel Size: Angle grinders come in various disc sizes, typically ranging from 115mm/4.5 inches to 230mm/9 inches. Select the appropriate size based on the scale of your projects. Smaller discs are ideal for precision work, while larger ones are better suited for larger surfaces and heavy-duty tasks. It comes in a wide range of sizes, and you need to choose the right size for the task you're going to be performing.
3. Speed Control: This feature allows you to adjust the speed to match the material at hand. Lower speeds are ideal for grinding and polishing, while higher speeds are essential for cutting challenging materials.
4. Safety Features: Prioritize safety by choosing angle grinders with essential safety features. Look for tools with adjustable side handles, which provide better control during operation. Additionally, models with kickback reduction and anti-vibration features enhance overall safety and user comfort. Slow start, anti-kickback, and paddle switch are angle grinder features that help prevent injuries. Safety is always a priority when using any power tool, make sure you follow these steps: Always use safety guards in the correct location. Always use side handles for stability.
Always wear gloves and goggles. Do not leave the grinder powered on when replacing the grinding discs. When the first installed wheel is defective, run the new wheel for one minute.
5. Durability and Build Quality: Choose a robust and durable angle grinder. Choose a model with sturdy construction and high-quality materials to ensure longevity, especially if you have demanding projects that require continuous use.
6. Ergonomics: Consider the ergonomics of your angle grinder, as this directly affects user comfort and control. Choose tools that are comfortable to hold and have a well-balanced design to minimize fatigue during prolonged use.
At KYNKO, we pride ourselves on offering a wide range of angle grinders that combine cutting-edge technology with durability and safety features. Explore our collection and choose the perfect angle grinder to elevate your projects to new heights.
Following are some of our best angle grinders,
KYNKO 115/125mm variable speed industrial angle grinder
1. 360 degree cooling system, effectively control the temperature rise.
2. Advanced manufacturing technology of motor, 900W strong power.
3. Using the patented coating technology to extend the motor life.
4. Variable speed with constant power protection, won't break under heavy duty work.
5. Easy assembling & disassembling design of dustproof insert, effectively protect the motor from dust.
6. Ergonomics design, Slim body, easy to grasp, flexible operation.
7. Runs smoothly at high speed, no vibrating to hand.
8. 20CrMnTi gear to reduce noise and increase life span
9. Application: stone, tile, metal, etc. materials cutting and grinding. Long life span, design for heavy duty.
1. Paddle switch, safe operation.
2. Advanced manufacturing technology of motor, 1000W strong power.
3. Using the patented coating technology to extend the motor life.
4. Imported housing is material, heat-resistant, no crack, no deformation.
5. Runs smoothly at high speed, no vibrating to hand.
6. Application: Stone, tile, slate cutting. Long life span, design for heavy duty.
1. 360 degree cooling system, effectively control the temperature rise.
2. Special lock-on switch, with soft start & restart protection. Safe and user friendly.
3. Advanced manufacturing technology of motor, 1600W strong power.
4. Using imported carbon brush, which life span is higher than 200 hours.
5. Using the patented coating technology to extend the motor life.
6. 20CrMnTi gear to reduce noise and increase life span.
7. Ergonomics design, easy to grasp, flexible operation.
8. Application: Metal, tile, stone, etc. grinding & cutting. Long life span, design for heavy duty.
1. 360 degree cooling system, effectively control the temperature rise.
2. Advanced manufacturing technology of motor, 2600W strong power.
3. Using the patented coating technology to extend the motor life.
4. 20CrMnTi gear with 2 time heat treatment to reduce noise and increase life span.
5. Ergonomics design, easy to grasp, flexible operation.
6. Using imported carbon brush, life span is higher than 200 hours.
7. Runs smoothly at high speed, no vibrating to hand.
8. Application: Metal, tile, stone, etc. grinding & cutting. Long life span, design for heavy duty.
The dryer scraper is a crucial component used in paper equipment and is typically made of phosphor bronze.
Why we use only phosphor bronze material for this scraper, here we have the answers:
We have the advantages on this specially designed alloy material like:
Corrosion resistance: Phosphor bronze exhibits excellent corrosion resistance, allowing it to be used in humid and chemical environments for extended periods without damage.
Outstanding wear performance: Phosphor bronze has good wear resistance, enabling it to endure high-speed scraping for extended periods, reducing blade wear and lifespan reduction.
Good conductivity: Phosphor bronze is a good conductor of electricity, providing excellent grounding conductivity in paper machine equipment.
Superior elasticity and hardness: Phosphor bronze possesses suitable elasticity and hardness, maintaining a stable shape and ensuring proper contact with the dryer surface.
In summary, phosphor bronze dryer scrapers possess excellent features such as corrosion resistance, good wear performance, conductivity, elasticity, and hardness. They are widely used in paper machine equipment for cleaning dryer surfaces, adjusting paper dryness, protecting the dryer surface, and enhancing production efficiency.
If you have any questions about this phosphor bronze dryer scraper, you're warmly welcome to contact Top We team.
Successful Injection Molding Service is an extremely complex undertaking, and the higher the complexity, the more expensive the mold becomes. Mainly include the following factors:
1. Material cost
Injection molds are subject to tremendous pressure and high temperatures. Therefore, the mold needs to be made of strong and durable materials so that it does not easily deform. These molds are typically made from different grades of steel or aluminum, raw materials that are inherently expensive.
2. Mold structure
Some complex parts need to be manufactured using molds. These parts are generally processed using imported professional machines to achieve strict tolerances, but the cost of imported machines is also very high.
3. Mold complexity and aesthetics
Some mold designs, strict tolerances, engravings, inserts, curves and other processes are relatively complex, making the finished product more refined and beautiful, but the production process is time-consuming and will also significantly increase the cost of the mold.
4. Labor costs
There are labor costs. Designing, manufacturing and assembling injection molds is a complex process that requires time and skill to be done correctly. Injection mold manufacturers and designers are experienced professionals, and their prices are also very high, which virtually increases the cost.
Recently, we received some inquiries from customers about dry-type transformers and oil-immersed transformers.
As you may know, dry-type transformers are generally more expensive compared to oil-immersed transformers. But why? What’s the difference between them?
Let Catherine explain it to you today!
Installation Location
Dry-type transformers are preferred for indoor locations such as basements, floors, and rooftops, especially in areas with high human population density oil-immersed transformers are typically used in substations.
Application
Box-type transformers are generally used for indoor applications, while oil-immersed transformers are commonly used for outdoor temporary power supply.
Space Considerations
The choice between dry-type and oil-immersed transformers depends on the available space. oil-immersed transformers are suitable for larger spaces, while dry-type transformers are preferred in compact spaces.
Climate: oil-immersed transformers are more suitable for humid and hot environments. If dry-type transformers are used in such conditions, they must be equipped with forced air-cooling systems.
Appearance
Dry-type transformers have visible cores and coils, while oil-immersed transformers are enclosed and only the outer shell is visible.
Connection
Dry-type transformers mostly use silicone rubber bushings, while oil-immersed transformers often use porcelain bushings.
Capacity and Voltage
Dry-type transformers are mainly used for distribution purposes, with capacities up to 1600 KVA and voltages below 10 KV. oil-immersed transformers can handle all capacities and voltage levels, including high voltage such as 1000 KV.
Insulation and Cooling
Dry-type transformers use resin insulation and rely on natural or forced-air cooling, while oil-immersed transformers use insulating oil for insulation and heat dissipation through radiators or cooling fins.
Suitable Locations
Dry-type transformers are commonly used in fireproof and explosion-proof environments, often in large and high-rise buildings. On the other hand, oil-immersed transformers are typically installed outdoors with provisions for an "incident oil pit" in case of leaks or spills.
Load-Bearing Capacity
Dry-type transformers should operate within their rated capacity, while oil-immersed transformers have better overload capacity.
Cost
Dry-type transformers are generally more costly compared to oil-immersed transformers of the same capacity.
If you want to know more about transformer cores, especially hope to purchase some good transformer cores in China. Contact SHUNGE! We will be very glad to help!
Transformers use various types of cores, with the most common ones being E-type and C-type cores. What are the differences between these two types of cores? And in which applications are they commonly used? Today, SHUNGE will tell you all about it.
E-type and EI-type cores are widely used in the industry. One of their main advantages is that the primary and secondary windings can share the same core, resulting in a higher window utilization factor. The core also provides protection for the windings, making them less susceptible to mechanical damage. Additionally, E-type cores have a larger heat dissipation area and reduce magnetic field dispersion.
However, E-type cores also have some drawbacks. They tend to have larger magnetic resistance due to the presence of larger air gaps in the magnetic path, which reduces the overall performance of the magnetic circuit. Furthermore, E-type cores are prone to issues such as higher copper wire usage, greater leakage inductance, and susceptibility to external magnetic field interference.
C-type cores are manufactured by winding cold-rolled silicon steel strips, which are then subjected to heat treatment and impregnation processes to form closed cores. These closed cores are then split to create two C-type cores. The windings are then encapsulated within the cores, and a pair of C-type cores are assembled and secured together to form the transformer.
C-type cores can have very small air gaps, and they offer advantages such as smaller size, lighter weight, and higher material utilization.
So, how can we identify the type of transformer core used in a power supply?
1. Identification based on appearance:
E-type cores have a shell-like structure, with a core that wraps around the coils. They are commonly made of high-quality silicon steel sheets such as D41 and D42. C-type cores, on the other hand, are made of cold-rolled silicon steel strips and have a core-type structure.
2. Identification based on the number of winding terminals:
Power transformers often have two windings, a primary and a secondary, resulting in four terminal connections. Some power transformers may have an additional shielding layer between the primary and secondary windings for AC noise and interference suppression. In such cases, the shielding layer is grounded. Therefore, power transformers typically have at least four terminal connections.
3. Identification based on the stacking method of silicon steel sheets:
In E-type power transformers, the silicon steel sheets are interleaved, with no air gaps between the E-shaped and I-shaped sheets. The entire core fits together tightly. In contrast, audio input/output transformers have certain gaps between their E-shaped sheets, which serves as a distinguishing feature from power transformers. C-type transformers are generally used as power transformers.
Shunge Steel, founded in 2008 and headquartered in Lecong, Foshan, produces cores with features such as low iron loss, high magnetic permeability, and high saturation induction. Our cores find applications in various fields, including signal communication, power drive, traction, renewable resources, charging station power control, high-precision measurement and control, new energy vehicle battery management, power control, welding, and new energy vehicle motor control.
If you have any core requirements, please feel free to contact us.